Contact between dissimilar metals – like copper fittings threaded into steel pipe or copper flashing fastened with steel nails – sets up an electro-chemical reaction that causes corrosion and leads to failure of the “less noble” metal
This video is aimed at ocean-drilling oil rig personnel, but it’s as clear an explanation of why dissimilar metals corrode when they come in contact as we could find. Below is a lightly edited version of the audio track. We’ve also pasted in a galvanic series chart in case it’s hard to read the one shown in the video. Remember, when fastening metals (such as pipes or flashing), try to use metals that are close together in the galvanic series.
Much of the equipment that is used in the oil industry is bolted in place, often at height. Here it is exposed to adverse weather conditions. If we choose the incorrect method of securing the equipment, galvanic corrosion may occur and the equipment may fall down. This happened on a relatively new platform where sound boards weighing five kilograms fell down just a couple of years after they were installed. The boards were fastened directly to the steel structure using aluminum hot rivets. The boards fell down due to galvanic corrosion.
But what is galvanic corrosion? Galvanic corrosion occurs when two different metals or alloys with different nobilities and therefore different electrochemical potentials come into contact with each other under water or in a damp environment. In the event of such contact, the less noble metal acts as an anode, and the more noble metal acts as a cathode. It is always the anode that corrodes
If a normal galvanized steel screw is used to secure equipment made of stainless steel, the screw becomes an anode, since the stainless steel is more noble. The greater the cathode area in relation to the anode, the faster the anode will corrode. In our example, the screw will corrode quickly, not only because the cathode is larger but also because the electrochemical potential is great. Note that galvanic corrosion may also occur between parts of the same metal if the parts are situated in different surroundings, such as areas with different pH values. For this to happen the anode and cathode must be in electrical contact with each other.
Galvanic Series
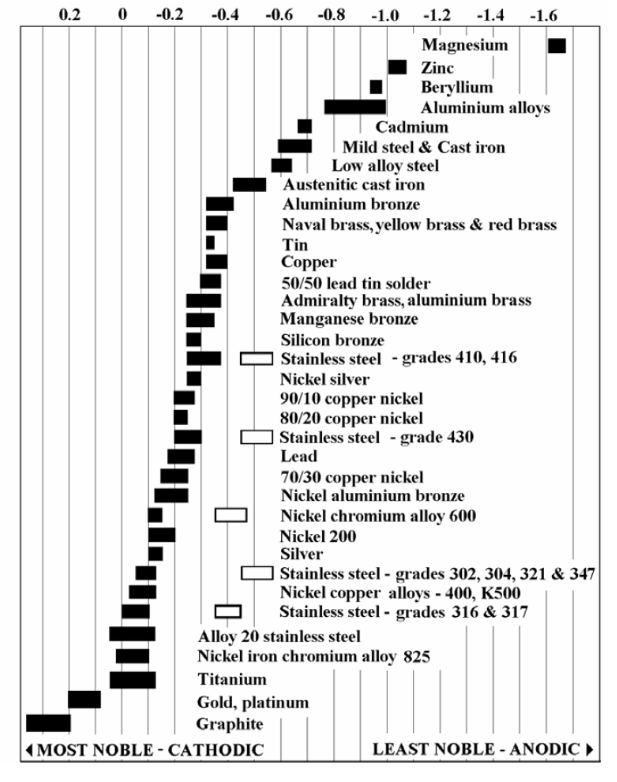
How can you prevent galvanic corrosion when designing or installing new equipment? For example, how do you choose the correct bolts to install an aluminum sign at height? Many of us would be happy if we found a bolt with the right length and an appropriate diameter, but is this good enough? We would also expect a high-quality bolt to ensure a high-quality installation, but is this always correct?
If using acid resistant or galvanized steel bolts to secure aluminum, you should use a nonmetal washer to isolate the metals from each other. Otherwise the aluminum may act as an anode and corrode around the bolt. The connection will then be weakened in the event of additional external stresses, such as wind. In this case, the sign may work loose and fall down while the bolt is left behind. Remember that a weakness of the isolating washer may be that the screws or bolts lose their pre-tension.
Here are some points of good practice to prevent galvanic corrosion.
1) Obtain an overview and select the correct bolts. Review the types of materials used in the equipment and structure to which the equipment will be fastened. Choose bolts that are appropriate to the relevant load and surroundings.
2) Use metals with the same or almost the same nobility.
3) Avoid contact between different materials. If you must use different materials, use washers to prevent the materials from coming into direct contact with each other.
4) Use paint as a buffer. An alternative method of preventing contact between the materials is to paint the surface. Remember to paint the most noble part, the cathode. If you paint the anode and a crack forms in the paint, the galvanic current will flow to this point may result in significant corrosion. Note that cranks in galvanized materials may also result in similar problems.
5) The size of the cathode matters. The size of the cathode circuit area exposed to water or another fluid determines how quickly the anode will corrode.
6) For piping, follow the pipe spec. For piping connections, follow the pipe spec to ensure that bolts and packing rings used in flange joints are made of the correct material.
7) When connecting piping of two different materials, consider using isolation spools. In sea water systems the isolation spools should be at least ten times the piping diameter. The isolation spools must be non conductive such as GRP or treated internally, such as with an epoxy paint or vulcanized rubber. Isolation spools are not recommended on hydrocarbon bearing piping.
8) Consider using sacrificial anodes in order to protect metals in seawater and thereby prevent corrosion.
9) Frequent inspections can also help to prevent galvanic corrosion causing accidents or near misses.
—Collaboration for Safety (Samarbeid for Sikkerhet) is a Norway-based public-private collaboration dedicated to improving safety in the oil and gas-industry.